The Quality Management Representative (QMR) is also called the quality representative or “management representative” by ISO 13485.
In this article, you will learn which tasks the person with this role is responsible for within an organization and which regulatory requirements must be observed.
1. Regulatory requirements
a) Requirements of ISO 13485
The requirements of ISO 13485 (“Medical devices – Quality management systems – Requirements for regulatory purposes”) for the Quality Management Representative can be found in ISO 13485:2016 in Chapter 5.5.2.
Quality Management Representative: organizational integration
The standard requires the organization to appoint a QMR, who must be a management member. However, this does not mean that the Quality Management Representative must be a managing director or located at the C-level:
Most organizations do not have a Chief Quality Officer. And if they do, that’s the quality manager, not the Quality Management Representative. You can read more about the difference between the two roles below.
In most cases, the QMR is a member of the extended management circle and reports directly to the management (C-level). ISO 14969 (“Medical Devices – Quality Management Systems – Guidance on the Application of ISO 13485”), as an “interpretation standard” for ISO 13485, at this point, even distinguishes between management and top management.
The standard primarily ensures that the QMR has sufficient time and no conflict of interest.
Quality Management Representative: Responsibilities and authorities
ISO 13485 requires that the management representative assumes the following responsibilities and tasks:
- The QMR must ensure that the processes required by the standard exist in the company and are practiced.
- The QMR must inform the top management about the “state” of the QM system and suggest if it should be improved.
- In addition, the QMR must help to ensure that colleagues are aware of how important it is to comply with the requirements of customers and regulations.
The QMR may delegate his tasks to third parties. However, he remains responsible for ensuring that tasks are completed.
b) ISO 9001 requirements
The 2015 version of ISO 9001 has removed the requirement for a Quality Management Representative. In this way, the standard aims to place greater responsibility on top management. This is to avoid shifting the responsibility to the QMR.
Of course, top management may delegate tasks – but not the responsibility for the quality management system.
Read more here about the differences between ISO 9001 and ISO 13485 (German).
c) FDA 21 CFR part 820
The FDA also recognizes the function of the Quality Management Representative:
820.20 (3) Management representative. Management with executive responsibility shall appoint, and document such appointment of, a member of management who, irrespective of other responsibilities, shall have established authority over and responsibility for:
- Ensuring that quality system requirements are effectively established and effectively maintained in accordance with this part; and
- Reporting on the performance of the quality system to management with executive responsibility for review.
These requirements are almost identical to those of ISO 13485.
Read more here about the Quality System Regulations of 21 CFR part 820.
With the FDA’s changeover to ISO 13485, 21 CFR 820.20 (3) no longer applies.
2. Quality Management Representatives: Typical tasks
The tasks of the QMR role depend greatly on the company’s size. The role covers almost all tasks in small companies, from writing standard operating procedures to investigating devices.
In medium-sized and larger companies, on the other hand, the QMR is the coordinator of the QM system. Several quality managers are employed in these companies – sometimes hierarchically at the same level (e.g., for different business areas), sometimes in a hierarchical management structure.
a) Task overview
The Quality Management Representative should perform the following tasks to meet the regulatory requirements.
Setting guidelines and planning
- If guidelines such as process or Standard Operating Procedures (SOPs) are missing, write these SOPs or delegate the task to the specialist departments.
- Draw up audit programs and audit plans.
- Coordinate and accompany external audits with the notified bodies. This also includes unannounced audits.
Check conformity
- Check that all regulatory processes and standard operating procedures have been established.
- Check existing SOPs for conformity with regulatory requirements.
- Monitor whether the organization is working in accordance with its SOPs. Quality Management Representatives usually conduct internal audits for this purpose.
- Conduct audits and document the outputs of audits in audit reports.
- Audit suppliers.
Support top management and other functional units
The Quality Management Representatives should support the top management in
- writing and updating the quality management manual,
- the management review,
- writing the quality policy, setting the quality objectives, and
- in “breaking down” these quality objectives to the organizational and operational structure (hierarchy, processes).
The tasks also include training colleagues (including management) on the importance and functioning of their own QM system and on regulatory requirements.
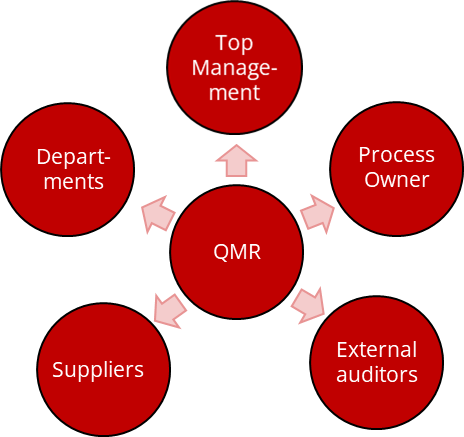
Read more about audits (in general) and about formulating quality objectives and the quality policy (German).
b) Delimitations and overlaps
Distinction from the regulatory affairs manager
Regulatory affairs managers are primarily responsible for product approval and compliance with laws. The quality manager or Quality Management Representative should ensure that the Standard Operating Procedures are written in such a way that they create records (e.g., technical documentation) that the regulatory affairs managers can use to compile the approval documents quickly and easily.
Both functions should coordinate, for example, to consider regulatory changes.
Distinction from process owners
Process owners are the roles that describe and update the content of the Standard Operating Procedures. On the other hand, the Quality Management Representative is responsible for conforming the SOPs with the regulatory requirements.
QMRs often coordinate the training required when changes are made, while process owners are responsible for their content.
Frequently, however, QMRs are also process owners of processes such as
- control of documents and records
- internal Audits
- corrective actions
- preventive actions
Distinction from top management
The top management bears the ultimate responsibility for the effectiveness of the QM system. The Quality Management Representative supports the top management in this within the framework of the tasks mentioned above.
Distinction from the quality manager
The role of the quality manager is not as clearly defined and established as that of the Quality Management Representative. For this reason, among others, the distinction between the two roles is not always completely clear. Often, the two terms are even used synonymously, which is not entirely correct:
The role of the quality manager is mainly found in larger companies. Quality managers pursue more strategic tasks such as:
- Improve the efficiency (time and cost) of processes
- Coordinate quality initiatives, e.g., Six Sigma program, lean management, and employee involvement
- Select and use quality and management tools such as portfolio diagrams, network diagrams, histograms, quality control charts, and many more
- Develop proposals for improving the organizational structure (hierarchical structure) and process organization (processes and their interaction)
- Take initiatives to secure and improve knowledge in the company systematically
- Coordinate interaction with other management systems (e.g., environmental management, occupational safety)
- Promote strategic customer and supplier relationships to improve quality
Distinction from the Person Responsible for Regulatory Compliance (PRRC)
The MDR and IVDR require a Person Responsible for Regulatory Compliance (PRRC) in Article 15. Even though in smaller companies, both roles are performed by one person, the two roles are not identical.
Responsibility | QMR | PRRC |
Ensure conformity of medical devices | (x) 1) | x |
Responsibility for technical documentation (including its up-to-dateness) | (x) 1) | x |
Responsibility for Post-Market Surveillance | (x) 1) | x |
Report to authorities | — | x |
Ensure that processes are defined and practised | x | (x) 2) |
Inform top management about the status of the QM system | x | — |
Create awareness in the company about the importance of the QM system | x | — |
1) The QMR is jointly responsible for the conformity of the associated processes
2) The responsibility is limited to the processes mentioned in the first four lines
The article on the responsible person describes their activities, competences, and regulatory requirements.
3. Competencies and training
a) Necessary competencies
Quality Management Representatives must have a vast range of competencies and capabilities:
- Precise knowledge of regulatory requirements, particularly ISO 13485 (or ISO 9001) and medical device law
- Audit techniques
- Analytical capabilities
- Moderation skills: QMRs must understand and be able to moderate the interests of top management, quality management, and technical departments
- Problem-solving skills and understanding of operational processes
- Persistence
Many Quality Management Representatives find it challenging that they must simultaneously
- check and guarantee the stringency of the QM system,
- not be perceived as an obstructive supervisory authority and a necessary evil, and
- make quality management understandable as something that helps the company: to offer devices and services faster and in better quality through clear agreements.
b) Training
The title of the Quality Management Representative is not protected. Therefore, anyone is free to offer appropriate training. Lecturers at the Johner Institute are also trainers of notified bodies and members of standards technical committees.
Gain the competencies as a Quality Management Representative with the Medical Device University:
- The MDU can be used perfectly for training and further education in regulatory affairs and quality management.
- Instead of attending numerous expensive and time-consuming basic training courses and advanced seminars, you develop the necessary competencies independently – at your own pace, from wherever you want and exactly when you need it.
- Benefit from the personal certificates as proof of competence in your QM system and thus ensure audit success.
Through our seminars on ISO 13485 or training as an ISO 13485 Lead Auditor, you can deepen your knowledge in the group.
4. External Quality Management Representative
Ideally, the Quality Management Representative should be a fixed executive of the company. However, there are situations in which it makes sense to have the possibility to collaborate with an external Quality Management Representative, at least temporarily. It is possible from a regulatory point of view.
It would be best if you considered an external Quality Management Representative in the following situations:
- Your company is small. A four-eye principle is not feasible.
- The competence is not sufficiently available in the company.
- The QMR is unavailable, for example, due to illness or termination.
- An appreciation of the QMR does not characterize the company culture. It is easier for the “prophet” from outside.
Read more here about how we can support you with an external QM Representative
Change history
- 2023-08-15: Notes on the FDA’s changeover to ISO 13485 added to chapter 1. c). Chapter 2. a) better structured by subheadings. Distinction from PRRC added to chapter 2. b).
- 2023-05-31: Editorial revision