The QM manual is the top document in the document pyramid of the QM system. It is an entry point for employees and auditors to get a quick overview of the QM system.
In this article, you will learn when you need a QM manual, its objectives, and what it should contain.
You will also find a template to download in this article.
1. QM manual: Objective and purpose
The QM manual is intended to serve as a central entry point for people who want to get to know the entire QM system, such as employees, auditors, and customers. The manual should provide:
- Overview of the contents and structure of the QM system.
- “Philosophy,” the values, and the quality policy of the company.
- Interaction of the processes
Since the QM manual does not yet describe company secrets such as concrete procedures (but only references them), some companies pass the QM manual on to customers.
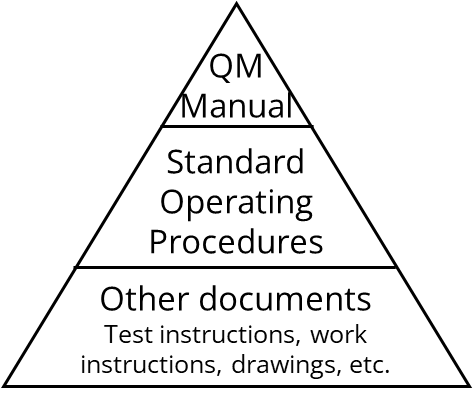
2. Content of the QM manual
a) Overview
The QM manual typically contains global specifications, particularly the quality policy and the quality objectives. It also gives an overview of
- the organizational structure of the company
- the document structure of the QM system
- the roles occupied within the framework of this QM system (but does not name specific persons).
Sometimes, the companies integrate the standard operating procedures into the QM manual.
You can read some arguments for and against the integration of standard operating procedures in the QM manual here and more about writing a company-specific quality policy and quality objectives (German).
b) Example of chapter structure
The Johner Institute regularly uses the following chapter structure for its customers’ QM manuals in its customer projects:
- Purpose
- Scope, responsibility & exclusions
- a) Scope
- b) Responsibility
- c) Applicable standards, guidelines & laws
- d) Exclusions & non-application
- About us
- a) Our company
- b) Our Quality policy and quality objectives
- c) Our organisation & roles
- Structure of the QM documentation
- a) Quality management manual
- b) Procedures and work instructions
- c) Other specification documents
- d) Records
- Processes
- a) Process overview & interaction
- b) Management processes
- c) Core processes
- d) Supporting processes
- General rules
- a) Internal communication
- b) Customer property
- Appendix
- a) Relevant documents
- b) Glossary
You can download an excerpt of a QM manual as a template here.
3 Regulatory requirements
a) MDR, IVDR
The EU Medical Device Regulations MDR and IVDR require a quality management manual in Annex IX (e.g., in Section 2.2):
Implementation of the quality management system shall ensure compliance with this Regulation. All the elements, requirements and provisions adopted by the manufacturer for its quality management system shall be documented in a systematic and orderly manner in the form of a quality manual and written policies and procedures such as quality programmes, quality plans and quality records.
MDR Annex IX, Section 2.2.
b) ISO 13485
ISO 13485 also insists on such a manual in Chapter 4.2.2 (“Quality management manual”). It must regulate:
- Scope of application (also exclusions)
- Procedures (can also be done by reference)
- Description of the interactions of the processes
- Structure of the documentation
4. Tips for the QM manual
a) Avoid typical mistakes
“No, I don’t think so” is the answer some QM officers give when asked if they think the manual will ever be read.
Thus, quality management has become a completely meaningless institution, even hindering the actual work. A look at the QM manual makes it possible to understand why no one ever wants to read it.
- Meaningless QM objectives
The company wants satisfied customers!? Really!? That should be obvious. But what makes this company unique? What can it do better than its competitors? What do customers appreciate about it? - Unspecific and incomplete
The business activities state that medical software would be developed. This is not surprising for a company that develops medical software. Does it also provide support? Does it run the application itself? Does it conduct training courses? Does it carry out installations at the customer’s site? If not even the company knows or describes exactly what it does, what should be in the manual? - Vague
The QM manual adopts the standard requirements largely unchanged. Any practical guidance is missing. No templates, no tools, no quality metrics. The same manual could have been applied to a logistics or cleaning company.
Such manuals are worthless.
In the article on quality policy and quality objectives (German) you will find practical and specific examples and suggestions.
b) Top-down approach
However, the problem with the creation is usually not (only) the QM representative but the management level. Because QM also works top-down:
- The management must clarify what the company is all about. What its philosophy and objectives are. You can also call this vision and strategy.
- Derive the quality policy from this. If a company wants to be the cost leader, a different policy is needed than for a company where patient safety is the priority.
- The quality objectives are derived from the quality policy. For each quality objective, one or more metrics are defined. And a target value for each of these metrics.
- Then, the business activities are determined and described, especially the services and devices provided for the customer.
- Then, the (internal) processes to create these services and devices are described. For example, the creation of medical software certainly includes processes such as risk management, usability engineering, and software development.
c) Consider further information
If you are unsure how to establish an effective QM system, don’t hesitate to ask us.
Contact the QM experts of the Johner Institute
Get comprehensive guidance on building a lean and compliant quality management system with our video training and dozens of templates in our Medical Device University.
Change history
- 2023-08-16: Chapter with regulatory requirements added. Editorial changes
- 2018-05: First version created