The digitalization of the production is an essential part of the digital transformation of manufacturing companies. However, not all companies benefit to the same extent from digitalization.
This article describes,
- how much the savings typically are worth,
- which companies benefit in particular, and
- how manufacturers should proceed with the digitalization of their production.
1. What is the digitalization of the production?
The digitalization of the production covers two areas:
- the automation of activities, e.g., by robots
- the support of employees in manual activities through good information logistics

This article focuses on the second aspect, the support of manual activities through information logistics.
Instead of work instructions on paper, an employee in the assembly receives precise instructions on a screen. These instructions are specific to the device to be assembled and to each work step. The next work step is explained, and immediate feedback is given as to whether the employee has carried it out successfully.
2. Why is the digitalization of the production important?
A process-oriented digital information logistic replaces routing slips, handwritten documentation, and static instructions. It offers many advantages over paper-based working methods:
- process reliability: fewer errors (minus 20 to 70 % manual errors)
- process efficiency: Higher productivity (plus 15 to 40 %)
- greater flexibility thanks to shorter training times
- greater satisfaction and motivation of operational employees, e.g., through modern workplaces, rapid feedback, and a sense of achievement
- transparency and responsiveness in ongoing operations
- traceability: Seamless proof of process and quality
Process reliability and traceability, in particular, have a positive effect on the conformity of production, which is required by law in regulated industries, including the production of medical devices.
The information that guides action …
- enables faster assembly
- reduces rework
- eliminates the need for troubleshooting
- reduces the number of rejects
- eliminates manual documentation of activities and reviews
Typically, this can save between EUR 7,000 and EUR 20,000 per workplace per year. This quickly results in a potential of EUR 50,000 to EUR 200,000 for a production area or production line.
The digitalization of the production is also an important tool for dealing with the shortage of skilled workers:
- On the one hand, it also enables less specifically trained people to carry out the activities.
- On the other hand, it reduces the number of people required.
By consistently collecting and processing information, companies collect a wealth of data they can evaluate using process mining. The objective is to solve new problems and further improve processes.
3. Who benefits from this digitalization?
The digitalization of the production is a plus for:
- companies that manufacture devices with short product life cycles, for example, because they have to keep up with the competition or the products are subject to frequent technical changes
- companies whose devices have to meet high-quality requirements
- companies whose production has a noticeable impact on profitability
- companies where comparatively demanding activities have to be carried out by people with a low level of training
- companies that are subject to high regulatory documentation requirements
4. How can the success of the digitalization of the production be achieved?
Tip 1: No infatuation with technology
Determine the expected return on investment (ROI) before starting the project.
Do not strive for digitalization purely out of a love of technology! The potential can be assessed at a very early stage and continuously reviewed over the course of the transformation project.
Tip 2: Proceed in phases
Implement your digitalization project in these four phases/steps:
- quantify potentials, calculate ROI (see tip 1)
- analyze existing processes (important!)
- derive a suitable solution from the analysis
- implement this solution
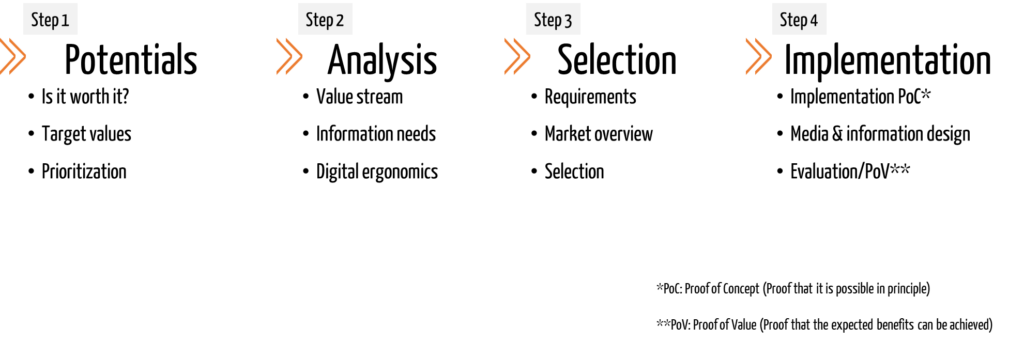
Tip 3: Involve employees at an early stage
You should involve all those affected, especially in phase 2 (analysis):
- Employees in production can contribute their expertise to finding a solution. As they are the ones who will later work with the solution, this also ensures acceptance of new processes.
- The IT department should be involved in the project at an early stage in order to be able to realize the technical implementation and participate in its validation.
- Quality management is necessary because process and work instructions usually have to be adapted.
- If necessary, the works council should be informed if data is collected that allows conclusions to be drawn about employee productivity.
Tip 4: Carry out the analysis bottom-up
If you want to improve processes, you need to understand them. This is rarely possible if you only look at them “from above.” Rather, it helps to observe the processes during ongoing production, record data, and interview employees.
The term “going to Gemba” is used for an analysis at the point of production.
The analysis results serve as a basis for discussion with middle and upper management to identify uniform and effective solutions.
Tip 5: Optimize processes “end-to-end”
A local optimum is of little help to your company. You should analyze the entire process chain across departments and use this understanding to optimize it piece by piece.
Therefore, do not limit your analysis to production or even individual work steps but to the entire process of value creation:
- from the customer’s order to
- order creation and
- work preparation through to
- production/manufacturing and
- dispatching.
Information analysis is an important method for analyzing process chains in their entirety.
As an output of this analysis, you have identified and clarified
- data sources and data sinks (both the type of data and the people/roles that generate or require this data)
- type of data generation (electronic, manual)
- transport of this data (paper, electronic)
- the actual data requirements
At the end of these activities, you will have a clear target picture of the future process and “information logistics.”
Tip 6: Identify and fulfill regulatory requirements
In regulated markets, in particular, you, as a manufacturer, must fulfill legal and normative requirements. These include the requirements:
- validation of computerized systems (CSV) – also in terms of 21 CFR part 11
- process validation
- competence of employees
- control of documentation (instructions) and records (e.g., to demonstrate the regulatory requirements for the devices produced)
- data protection (including roles and access rights)
- IT security
The Johner Institute keeps you up to date with further articles on computerized systems validation (CSV), process validation and IT security.
Do not underestimate the effort involved, especially for validation. Remember to take this into account in your project planning and ROI calculation.
- The validation of processes and systems presupposes that the requirements for these processes and systems are specified in a testable manner.
- Another prerequisite is the inventory of the systems and components involved and the specification of their interfaces.
- Validation should be risk-based, which requires a risk analysis (also in the sense of ISO 14971).
- Validation is an ongoing process that continues into the operation of the systems. Therefore, error messages should be collected, the systems should be revalidated in the event of changes (e.g., updates), and error logs should be evaluated.
Tip 7: Make an informed “make or buy decision”; benefit from tools
There is a wide range of systems on the market to help you digitalize the production:
- Digital Assistance Systems (DAS, also known as worker guidance employee information systems) are software solutions to provide operational employees with the process of the presentation of task-relevant (!) information.
- The functionally more comprehensive Manufacturing Execution Systems (MES) often also have individual modules with comparable functions.
DAS support employees
- in recognizing the correct work steps (especially with high product variance through context recognition),
- with process documentation and
- in process control,
- by outputting the appropriate information (e.g., also during training and familiarization), and
- through data collection and analysis (e.g., as part of a real-time quality evaluation).
The systems available on the market have different combinations of the functions described. You should know exactly what your requirements are before you decide to purchase or license a system.
Only use systems that allow you to demonstrate compliance with the regulatory requirements.
5. Summary and conclusion
The digital transformation of companies also includes the digitalization of the production. If the ROI for this digitalization is worthwhile, tools available on the market will help in most cases. However, these tools need to be validated and should only be considered after an analysis phase.
Manufacturers in regulated industries, such as medical device manufacturers, benefit the most from the digitalization of the production.
The Johner Institute supports medical device manufacturers in determining regulatory requirements (including in the production) and in the validation of processes and computerized systems. Please feel free to contact us.To ensure the successful completion of the project, AssistIng supports manufacturers in all industries with potential and process analysis, process optimization, tool selection, and project management.